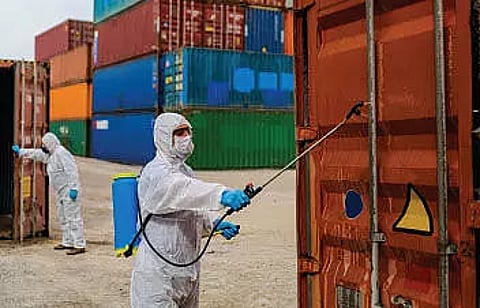
Dr B K Mukhopadhyay
(The author is a Professor of Management and Economics, formerly at IIBM (RBI) Guwahati. He can be contacted at m.bibhas@gmail.com)
Dr. Boidurjo Rick Mukhopadhyay
(The author, international award-winning development and management economist, formerly a Gold Medalist in Economics at Gauhati University)
The growth of 'Electronic Retails' or simply e-tails (e.g., Alibaba, Amazon, etc.) transformed business-to-consumer (B2C) e-commerce for both the SMEs and large corporations, it has also evolved the conventional market structure due to the online platforms continually tailoring to 'instant gratification' and meeting the changing needs of customers.
Due to the imposed challenges and restrictions on logistics and procurement network since the pandemic hit, there has been several changes in the process and also the supply-chain risk management, the emergence of the new e-tail supply chain model, and the increasing use of AI (Artificial Intelligence) as well as the automation at warehousing and procurement facilities.
The changing situation posed quite a few questions to ponder on -- for example, for the omnichannel businesses (who has both physical stores and also the online platforms where consumers could order and have it delivered at doorstep), could delivery be cheaper and faster if some e-Tails make online orders available or 'pick up at our store' delivery only? Would it be more economical to keep the delivery operation in-house or outsourced? What new strategies need to be crafted to better manage return orders and failed deliveries?
Global manufacturing value-added output suffered significantly last year. In 2021, as things pick up very slow - this value is projected at 4% for Asia-Pacific (excluding China), 6% value-add for the US, and the pick-up in Europe is set at 5%. The transition from pandemic to pre-new-normal, and new normal - has been long and complex which also came with organisational learning of how immediately businesses need to mobilise rapidly, mitigate risks better, develop stronger crisis management mechanisms, and have resilience in supply chain and procurement management for business continuity.
The Changing Demand Patterns and Logistics Landscape: To ensure goods and services moving to the store shelves or warehousing facilities and customers' doorsteps came at a cost for e-tails and their logistics networks and also change in the process and management of the same. There has remained a shift in consumer purchasing patterns and clearly a huge spike in demand for the sale of food, household, and personal-care products as opposed to apparel and furnishing for example. Downloads of delivery apps for grocery retailers increased by 100 to 200 per cent last year, as per a report by McKinsey. Neither the stores, logistics systems, nor distribution facilities and supplier networks were engineered to respond to the rapid shift in demand patterns that the pandemic imposed.
At the same time, the pandemic had created temporary 'manufacturing deserts', whereby a city, region or when the whole country's output drops so substantially, where anything apart from essential items such as food and pharmaceuticals were not available or accessible. Naturally, the extended and repeated (in most places) shutdown of parts of the global market had impacted supply chains as existing stocks have depleted or expired. So, the immediate focus of businesses is to minimise supply chain disruption and to adjust to a changing landscape and renewed customer demand patterns. This encompasses implications on infrastructure, tax and employment (especially what kind of contract will be offered) and the option of reversing changes quickly when the 'new normal' phase initiates.
Across industries, there has been a strong focus on top-tier suppliers conventionally instead of lower-tier suppliers. And during the pandemic, the vulnerability and the shock came heavily down to lower-tier suppliers as any disruptions at that level impact the entirety of the supply chain. Lower-tier suppliers provide critical input to the production process which, when delayed or unavailable, sends a shock wave and losses in production. For industries with an extended supply chain – whether it's food and beverage, furnishing, or consumer goods, this becomes highly critical. For example, due to the reduced availability of 'made in China' parts, several automotive plants closed down in Japan and Korea towards the end of last year.
Supply Chain Strategies during the pandemic and post-pandemic phases: During summer this year, an increasing number of discussions started around a) lockdown period, b) pre-new-normal period; and the new normal. In regard to business focus for supply chain and logistics management during each of these phases, firstly for lockdown period, the pressing focus was on matching production to demand, managing costs and investments, staying close to customers, ensuring supplier readiness while also recognising and exploiting new short-term opportunities; during the second phase, the focus was largely to strengthen and reconfigure supplier network (global and 'glocal'), and also to reassess crisis scenario and devise emergency plans. At the same time, the choice was around whether to continue logistics and procurement using existing resources and networks or to consider alternative/ additional distribution channels.
Finally, while looking at the third phase which is the new normal, most industries in the business with expansive supply chain and logistics considerations have diversified in terms of new markets, new suppliers, refined business models, and also at times products and services that they offer. There is an increasing level of understanding of crisis and risk management and crafting new crisis-proof business models.
Looking at the overall strategies of organisations, 'resilience' is something that is certainly focused on a lot more now than in the past. As time passes and markets start to recover, businesses must learn to expect both regulatory and social pressure to ensure that they are more resilient to unexpected and medium to long term shocks with stocks maintained of critical products. In one of the international trade sessions recently, the European Commission has identified Europe's reliance on Asia for the production of personal protective equipment which is now slowly moving back to establish greater manufacturing capacity in Europe instead in case of another emergency re-purposing existing production lines.
Certainly, there is a huge risk in this too – because we cannot assume that the newly configured supply chain could provide how traditionally provided parts or materials were made available. Meanwhile, the pre-existing suppliers may have moved on to something else entirely during this period. Diversification does require the development of a completely new supply chain network and infrastructure while also assessing supplier health and readiness, including business continuity plans and contingency alternatives. For e-tails, this is a huge area of investment and focus as this alone guarantees their sustainability of the business.
Challenges for Shippers: The disruption in the supply chain increased transit times from the 'Port of Origin' to the destinations. For example, a report by UNICEF in November 2020 shows that a consignment from Copenhagen to Port Sudan took 60 days which is 50 per cent increases over the typical 40-day period. Severe congestion at global seaports delayed loading and offloading containers, and not to mention the colossal number of ships that were stuck at Chinese ports during the early pandemic period.
Transportation and workplace-related changes, e.g., WFH, connected with social distancing effect e-tails significantly. Logistics also involved people working in shipping offices, warehouses, cross docks, ports, and airports. For e-tails again, in particular, the warehouses and pick-up locations are densely populated. Not every warehousing facility are managed by AI and robots as found at Alibaba's in mainland China. But gradually, there is a big shift towards robotics and automation in the case of physical good handling. However, during this period the management of warehouses and picking locations experiences a sea change in the process. They had to reflect the requirements of the social distanced workforce, and changes such as one-way systems, distributed picking faces, social distanced packing areas, and hand-sanitiser stations.
Those businesses who shifted to automation by a large measure had their own measures to ensure that the systems are robust and capable of supporting a distributed workforce, and employees have access to appropriate data and systems. Regardless of which process (of the two, above), a firm chose to go with, there's been a constant re-assessment of the trade-off between lead-time vs transport cost, and the refined information systems will need to fully support a remote workforce.
Regardless of the roles that AI and automation will take on, supply chain risk management and sustainability logistics would still involve significant human intelligence as well as data collection and its organisation. To have a holistic picture of the fundamental structure of the supply chain as well as the key contacts, suppliers and stakeholder engagement along the supply chain specific to each company is a priority. Taking stock of the above while also constantly monitoring updated accounts of such information would help reduce vulnerability and find ways to mitigate, minimise, and manage these risks more pragmatically.