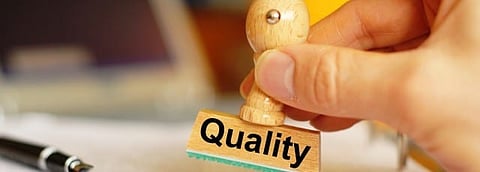
Ranjan K Baruah
We are all concerned about quality.Whether it is food or any other service, we need quality everywhere. Quality is important for each and every one of us. A student is concerned about quality education whereas a business person is concerned about quality business while a consumer looks for quality services and products. In business, engineering, and manufacturing, quality has a pragmatic interpretation as the non-inferiority or superiority of something; it's also defined as being suitable for its intended purpose (fitness for purpose) while satisfying customer expectations. Quality is a perceptual, conditional, and somewhat subjective attribute and may be understood differently by different people. Consumers may focus on the specification quality of a product/service, or how it compares to competitors in the marketplace. Producers might measure the conformance quality, or degree to which the product/service was produced correctly.
There are many aspects of quality in a business context, though primary it is the idea that the business produces something, whether it be a physical good or a particular service. These goods and/or services and how they are produced involve many types of processes, procedures, equipment, personnel, and investments, which all fall under the quality umbrella. Key aspects of quality and how it's diffused throughout the business are rooted in the concept of quality management. The main terms associated with quality are as follows:
Quality Planning: Quality Planning is implemented as a means of “developing the products, systems, and processes needed to meet or exceed customer expectations”. This includes defining who the customers are, determining their needs, and developing the tools (systems, processes, etc.) needed to meet those needs.
Quality Assurance:Quality Assurance is implemented as a means of providing enough confidence that business requirement and goals (as outlined in quality planning) for a product and/or service will be fulfilled. This error prevention is done through systematic measurement, comparison with a standard, and monitoring of processes.
Quality Control: Quality Control is implemented as a means of fulfilling quality requirements, reviewing all factors involved in production. The business confirms that the good or service produced meets organizational goals, often using tools such as operational auditing and inspection. QC is focused on process output.
Quality Improvement:Quality Improvement is implemented as a means of providing mechanisms for the evaluation and improvement of processes, etc. in the light of their efficiency, effectiveness, and flexibility. This may be done with noticeably significant changes or incrementally via continual improvement.
In today’s section of Career Corner, we are focusing more on Quality Assurance and how it can be a career option for our students. This is a relatively new term for many but as more and more people are getting concerned about quality, so, it is bringing more opportunities for young people in India. Quality Assurance (QA) is a way of preventing mistakes or defects in manufactured products and avoiding problems when delivering solutions or services to customers; which ISO 9000 defines as “part of quality management focused on providing confidence that quality requirements will be fulfilled”.
The terms “quality assurance” and “quality control” are often used interchangeably to refer to ways of ensuring the quality of a service or product. Quality assurance comprises administrative and procedural activities implemented in a quality system so that requirements and goals for a product, service or activity will be fulfilled. It is the systematic measurement, comparison with a standard, monitoring of processes and an associated feedback loop that confers error prevention. This can be contrasted with quality control, which is focused on process output.
Quality Assurance includes two principles: "Fit for Purpose" (the product should be suitable for the intended purpose); and "Right First Time" (mistakes should be eliminated). QA includes management of the quality of raw materials, assemblies, products and components, services related to production, and management, production and inspection processes. The two principles also manifest before the background of developing (engineering) a novel technical product: The task of engineering is to make it work once, while the task of Quality Assurance is to make it work all the time.
Historically, defining what suitable products or service quality means has been a more difficult process, determined in many ways, from the subjective user-based approach that contains “the different weights that individuals normally attach to quality characteristics,” to the value-based approach which finds consumers linking quality to price and making overall conclusions of quality based on such a relationship.
The quality of products is dependent upon that of the participating constituents, some of which are sustainable and effectively controlled while others are not. The processes which are managed with QA pertain to Total Quality Management. If the specification does not reflect the true quality requirements, the product’s quality cannot be guaranteed. For instance, the parameters for a pressure vessel should cover not only the material and dimensions but also the operating, environmental, safety, reliability and maintainability requirements
Aspirants seeking a career in Qualify Assurance Management should preferably focus on subjects like Mathematics, Statistics or Science. Graduates may try and plan their career in the field of Quality Assurance Management. There are certificate, diploma, bachelors, masters and post graduate courses which are offered by various colleges in India. The purpose of Quality Assurance Management courses is to make students familiar with all the important aspects of Quality Assurance Management. Aspirants may choose do further specialization after they finish their graduation courses and students from different fields, like pharmacy or agriculture or others, may come and choose to be in the field of Quality Assurance.
Quality Assurance managers can find job openings in varies fields like: Pharmaceutical Industries, Biomedical and Environmental sectors, IT and Software development companies, Shipping and Transport sectors, Engineering field, Manufacturing companies, Health care sectors, Commercial Goods, etc. After the successful completion of a Quality Assurance and Management course, one can work as Quality Assurance Managers, Quality Analysts, Quality Control Inspectors, Quality Assurance Officers, Quality Assurance Engineer, Quality Control Supervisor, Quality Researcher, Quality Assurance Technician, Quality Surveyors, Software Quality Analyst, Software Quality Assurance Engineers, etc.
Some of the courses related with Quality Assurance Management includes: B.C.A in Software Quality Assurance and Testing, B.Pharm Quality Assurance, B.Sc. Food Science and Quality Control, B.Sc. Food Science, Nutrition and Food Quality Control, Certificate Program in Quality Assurance in Clinical Research, Diploma in Quality Assurance Management, Diploma in Quality Control, Diploma in Quality Engineering (DQE), Diploma in Quality Management (DQM), Diploma in Total Quality Management, M.E. Quality Engineering and Management, M.Pharm Quality Assurance, M.S. Quality Management, Master of Science (M.Sc.) in Total Quality Management, MBA Total Quality Management, P.G. Diploma in Chemical Analysis and Quality Assurance, Post Graduate Diploma in Dairy and Food Quality Assurance, Post Graduate Diploma in Quality Assurance Management, Post Graduate Diploma in Quality Management (PGDQM), Post Graduate Diploma in Software Quality (PGDSQ), Post Graduate Diploma in Total Quality Management (PGTQM), etc.
Quality Council of India: The Quality Council of India (QCI) is a pioneering experiment of the Government of India in setting up organizations in partnership with the Indian industry. QCI was set up in 1997 by the Government of India jointly with stakeholders of the Indian Industry as an autonomous body under the administrative control of the Department to establish and operate the National Accreditation Structure for conformity assessment bodies; providing accreditation in the field of education, health and quality promotion.
Besides its role of putting in place an accreditation structure, it also promotes the adoption of quality standards relating to Quality Management Systems (ISO 14001 Series), Food Safety Management Systems (ISO 22000 Series) and Product Certification and Inspection Bodies through the accreditation services provided by National Accreditation Board for Certification Bodies (NABCB). The Indian industry is represented in QCI by three premier industry associations namely ASSOCHAM, CII and FICCI.
QCI has been assigned the task of monitoring and administering the National Quality Campaign – a plan scheme of the department, and also to oversee function of the National Information and Enquiry Services. To realize the objective of improving quality competitiveness of Indian products and services, QCI provides strategic direction to the quality movement in the country by establishing conformity assessment system which is recognized at the international level.
(Ranjan K Baruah is a social activist and career mentor who has conducted career awareness programme in different parts of Assam and Northeast India and can be reached at bkranjan@gmail.com or 8473943734 for any career related queries.)