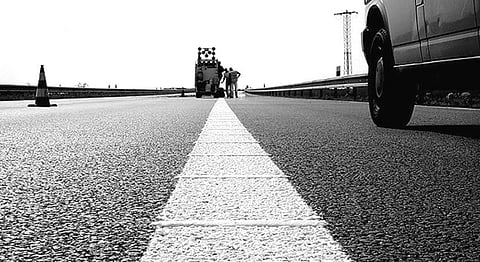
The total length of Indian roads including National highways, State highways, Urban roads, Rural roads, Project roads and PWD roads sums up to be more than 5472144 kms. On the other hand, more than 15,000 tonnes of plastic waste are generated in India every day, of which 6,000 tonnes remain uncollected and littered. Plastic garbage is commonly seen around the country and has started causing several problems. Plastic waste clogs drains, causing floods. It chokes animals who eat plastic bags, etc. Plastics found in fields blocks germination and prevent rainwater absorption.Recycling plastic can be done only 3-4 times and melting the plastic for recycling releases highly toxic fumes. What if we could make roads using waste plastic? We can, and it has proven to be a very efficient alternative to traditional ways of making roads
Jambulingam Street in Chennai, one of India’s first plastic roads, is a local legend. The tar road in the bustling Nungambakkam area has weathered a major flood, several monsoons, recurring heat waves and a steady stream of cars, trucks and auto rickshaws without showing the usual signs of wear and tear. Built in 2002, it has not developed the mosaic of cracks, potholes or craters that typically make their appearance after it rains. Holding the road together is an unremarkable material: a cheap, polymer glue made from shredded waste plastic.
The environmentally conscious approach to road construction was developed in India around 15 years ago in response to the growing problem of plastic litter. As time wore on, polymer roads proved to be surprisingly durable, winning support among scientists and policymakers in India as well as neighboring countries like Bhutan. “The plastic tar roads have not developed any potholes, rutting, raveling or edge flaw, even though these roads are more than four years of age,” observed an early performance report by India’s Central Pollution Control Board. There are more than 21,000 miles of plastic road in India, and roughly half are in the southern state of Tamil Nadu. Most are rural roads, but a small number have also been built in cities such as Chennai and Mumbai.
Adding flexible materials to strengthen tar roads is not a new idea. Commercially made polymer-modified asphalts first became popular in the 1970s in Europe. Now, North America claims 35% of the global market. Modified asphalts are made from virgin polymers and sometimes crumb rubber (ground tires). But even in the US, cost is a significant barrier. The most widely used polymer, styrene-butadiene-styrene, can increase the price of a road by 30-50%. In India, high-stress roads like runways and expressways are increasingly using polymer modified asphalts made by manufacturers like DuPont.
While polymer roads in the US are made with asphalt that comes pre-mixed with a polymer, plastic tar roads are a frugal invention, made with a discarded, low-grade polymer. Every kilometer of this kind of road uses the equivalent of 1m plastic bags, saving around one tonne of asphalt and costing roughly 8% less than a conventional road. Dr R Vasudevan, a chemistry professor and dean at the Thiagarajar College of Engineering in Madurai, came up with the idea through trial and error, sprinkling shredded plastic waste over hot gravel and coating the stones in a thin film of plastic. He then added the plastic-coated stones to molten tar, or asphalt. Plastic and tar bond well together because both are petroleum products. The process was patented in 2006.
The whole concept of making roads using waste plastic has been researched by many, since then. Companies like Macrebur, has taken the concept to a game-changing level. The idea was born when CEO, Toby, was working in Southern India with a charity helping people who work on landfill sites as ‘pickers’. Their job was to gather potentially reusable items and sell them on to be turned from rubbish into something useful again. Some of the waste plastics retrieved by the pickers were put into potholes, petrol poured all over them, and the rubbish set alight until the plastics melted into the craters to form a makeshift plastic pothole filler.
He got together with two friends, Nick and Gordon, and formed MacRebur and came up with the innovative idea to take a mix of waste plastics, pelletise them and add them into the making of an enhanced asphalt road. After 18 months of testing and trials, they had their product ‘MR6’, which is within British and European standards and is a patent pending, high performance, asphalt binder additive that enhances the roads we drive on today.
MR6 is stronger and longer lasting than standard asphalt. It increases lifespan of a road, reduces production costs & reduces maintenance costs. While there is currently no product available to reduce the costs of asphalt and make the roads stronger & longer lasting, MR6 pellets replace costly fossil fuel bitumen in the road mix.
Last year, the Indian government announced that plastic roads would be the default method of construction for most city streets, part of a multibillion-dollar overhaul of the country’s roads and highways. Urban areas with more than 500,000 people are now required to construct roads using waste plastic. This will also go hand in hand with the “Swachh Bharat Abhiyan”, plastic being the prime menace when it comes to cleanliness. India’s road upgrade is also long overdue. A recent road safety report by the World Health Organization (WHO) found that 17% of the world’s traffic fatalities occur in India, with crumbling roads partly responsible for the high death toll. In 2014, potholes alone caused more than 3000 deaths.
With the adoption of this techniques, we can indeed solve two major crisis of the recent times; Pot-hole prone roads and ever increasing plastic waste. Added to that, it will also drastically reduce the use of fossil fuels in traditional road making techniques.
By Manjit Kashyap
Also Read: Is Immortality Possible?